PLA Sheet Press
The purpose of the shredded plastic is to create flat sheets that can be laser cut or repurposed, similar to acrylic sheets. This is achieved by utilizing a t-shirt heat press with a mold. A mold is made up of a frame and a cover. Several mold composition combinations were considered, varying in materials such as Stainless Steel, Silicone, and Teflon. These materials were chosen for their thermal conductivity, cost, and manufacturability.
After a series of tests, it was determined that the best combinations include the stainless steel frame with either a Teflon or silicone cover. There were issues where the PLA burned or could not be removed from the stainless steel cover configuration. The stainless steel frame features a ⅛” border for consistent sheet thickness and was graciously manufactured by Brian Yudin in the machine shop at 41CS.
MAKING A PLA SHEET
The process of creating a PLA sheet begins with weighing the plastic material. In addition to the PLA scraps, PLA pellets used for injection molding can also be added as an additional binder due to their small size. We used the FilaBot LX175 PLA.
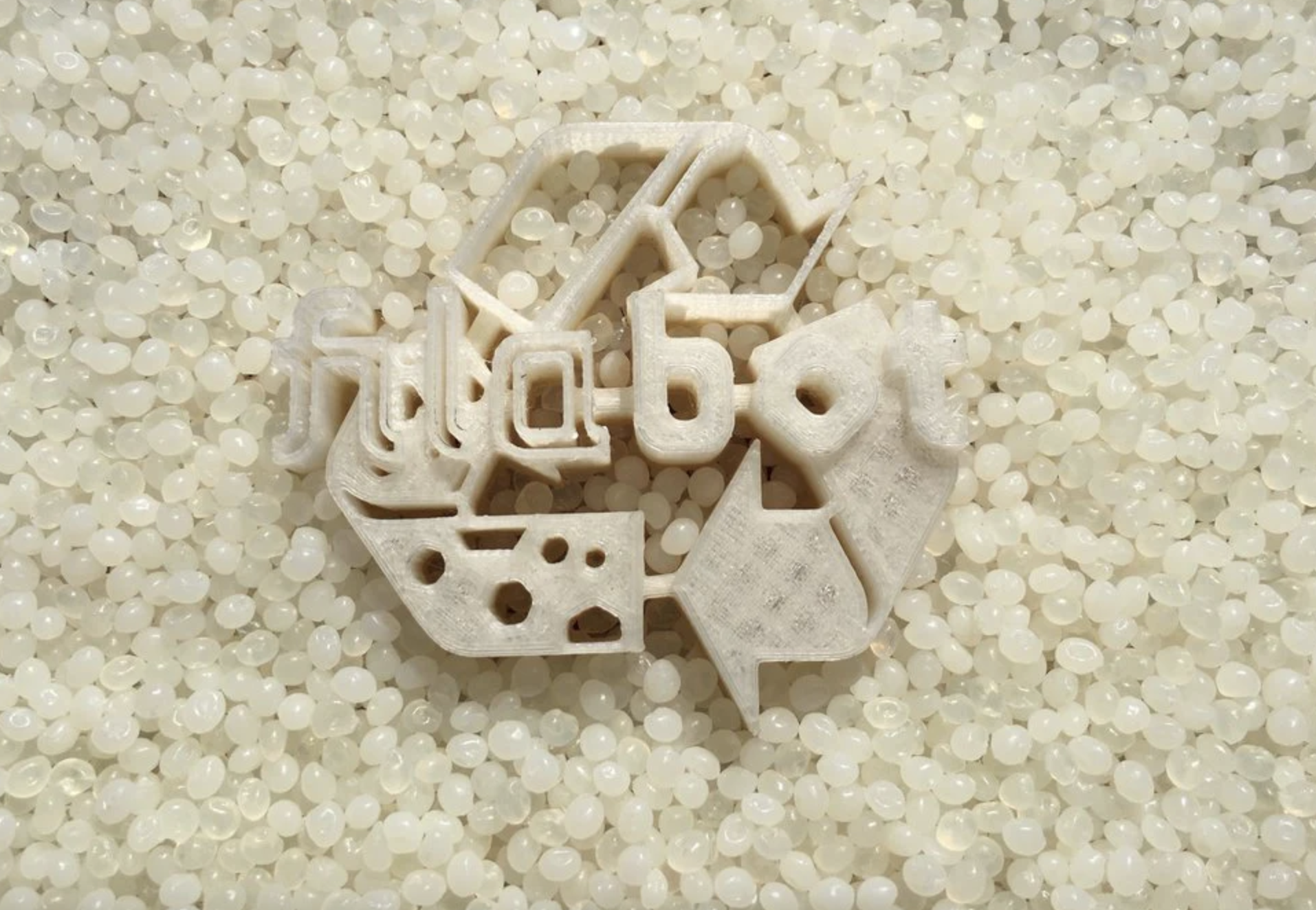
(image from Filabot.com)
Teflon vs Silicone Cover
The heat press can then be preset to a variety of temperatures and times. The processing temperature for PLA is approximately 200C, however through many experiments, higher temperatures are suggested to expedite the melting process. Through empirical observations, the sheet pressed needs to be heated at 450F (232C) for 10 minutes.
The sheet press must be lowered and closed to apply pressure and heat to the plastic. The melting process has to be monitored meticulously to prevent burning. When burning occurs, the PLA sheet will have inconsistent thickness and there will be fumes. It is important to note that proper safety precautions were taken, including wearing N95 masks and working in a properly ventilated area.
Once the heating time has passed, the sheet press is raised to allow the molds to cool for 1 minute. The cover sheet is then removed to avoid undesired adhesion to the cover plate, which could affect the surface finish quality. The molds are then removed from the press safely using Neoprene heat-resistant gloves in order to quench the back of the molds with the exposed PLA facing downwards. Cold water is run over the mold for 5 minutes. This may cause slight warping to the sheet but can be easily resolved with a heat gun.
Step 1. Place dry pellets and scraps into mold frame
Step 2. Place cover (silicone or teflon) over pellets and press @ 450F for 10 mins
Step 3. Remove cover and let cool
Step 4. (optional) Quench stainless steel frame
*ALWAYS TAKE PROPER SAFETY PRECAUTIONS
After the mold has finished cooling, the PLA sheet is complete! These PLA sheets can be used for a variety of creative purposes. Below are several examples:



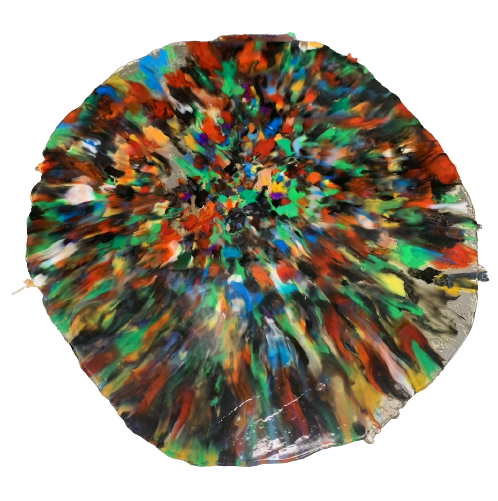